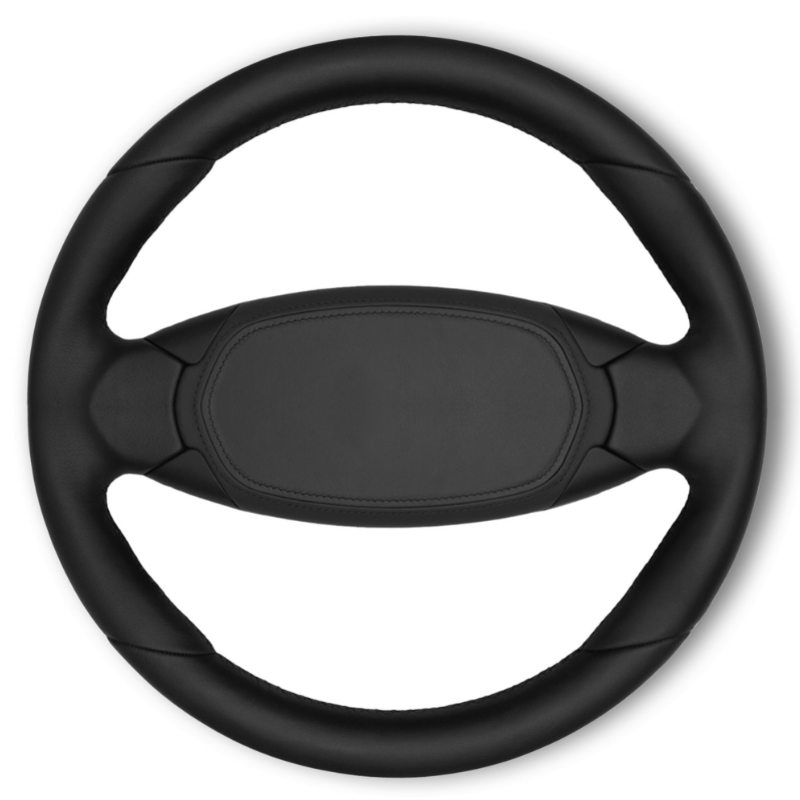
Automotive steering wheels have been around since the year 1894, and have ever since been an essential part of our everyday lives. The design of the steering wheel has seen continuous innovations throughout its time, and that includes the very materials which are used to make it.
Steering wheels are comprised of a thin rim, constructed from magnesium, aluminum, or steel, acting as the internal support. The rim is lined with a type of plastic; a hard molded plastic for wrapped steering wheels and injection molded polyurethane for non-wrapped steering wheels.
From an everyday driver’s perspective, without taking the structural materials into account, there are mainly 2 types of steering wheel materials in modern cars: Leather or Suede/Alcantara wrapped steering wheels and polyurethane steering wheels.
Materials used in a steering wheel
Framework Material
The rim material in a steering wheel, which serves as its structural support, is most commonly one of three alloy materials: iron, aluminum, and magnesium alloy.
The manufacturing process of a steering wheel’s internal support structure involves die-casting hot molten metal which is injected into a mould cavity in the shape of a steering wheel.
Iron Alloy (Steel):

Steel is an alloy of iron. Many of the older automobiles had steel steering wheels, mainly stainless steel. Classic automobiles had large steering wheels due to the absence of powered steering. Without power steering, steering wheels had to bear the full weight of turning the vehicle. This required a strong material that could handle these loads.
Classic vehicles also did not have the many layers of covering materials that modern steering wheels have today. Certain parts of the steering wheel were exposed, subject to the elements. As such, the steering wheel metal needed to be durable and resistant to scratches, corrosion, UV rays, and rust. All of which are hallmark attributes of stainless steel.
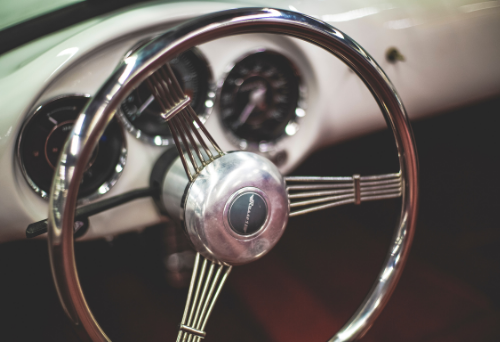
Steel is the most widely used material in the automotive industry, as iron is the most accessible and affordable metal resource in the world. According to World Auto Steel, the average vehicle is made of 65% steel by weight, 25% of which is recycled steel.
However, today, not many automobile manufacturers use steel steering wheels. The majority of steel steering wheel production is limited to the aftermarket steering wheel industry.
Aluminium Alloy:

The importance of weight reduction in vehicles become more and more important as automobile manufacturing progressed. Reducing the weight of a vehicle increases efficiency and performance. Aluminum, while very strong, is nowhere near as strong as stainless steel. However, what aluminum gives up in size, it makes up for in weight. Aluminum weights approximately 3 times less than steel does.
An aluminum steering wheel’s manufacturing process involves die casting. Hot molten aluminum is injected into a mould cavity in the shape of a steering wheel.
Many modern vehicles use aluminum in their steering wheels today. With the addition of powered and electric steering, steering wheels are much smaller than they used to be and require much less force to turn the wheel. As such, steel steering wheels are no longer as needed, compared to how they were a few decades back.
Working with aluminum is much easier than with steel as it is lightweight and very malleable. Aluminum is a softer and more deformable material, and the melting temperature of aluminum is about half of that of steel. Due to this, aluminum steering wheels are the more cost-effective and eco-friendly option.
One of the key benefits of using aluminum steering wheels instead of steel is the added safety factor. Aluminum is more ductile than steel, making it much better at absorbing/redirecting impact in the case of an accident.
Magnesium Alloy:
Magnesium-based car components are alloyed with other metals such as aluminum and manganese to stabilize magnesium’s unstable properties. Magnesium alloy steering wheels use AM50 (MgAl5Mn) and AM60 (MgAl6Mn) cast alloy.
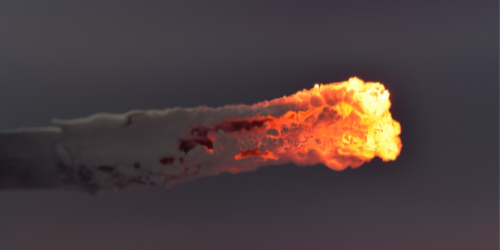
Although magnesium alloy’s lightweight properties are very advantageous, it is still quite reactive when compared to aluminum alloys and steel. For that reason, magnesium is used in parts of the vehicle which are not subject to high temperatures.
Most modern steering wheels today have armatures that are completely covered in plastic material. For this reason, magnesium could easily be used in the internal structure of a steering wheel without having to worry about its unstable properties.
Magnesium alloys, AM60B alloy, in particular, have an ideal combination of stiffness, strength, and shock absorption for steel wheels with airbag systems according to crash tests conducted by Toyota in 1991. Although other materials may perform fractionally better in crash tests, the benefit of weight reduction is the deciding factor.
Magnesium alloys offer many of the same benefits as aluminum when using it over steel, but at a much greater extreme in both advantages and disadvantages. Magnesium is 33% lighter than aluminum, but it is less durable. Its alloys are softer and more malleable than aluminum but are more expensive to produce.
Covering Material
Bakelite and Tenite (Hard Plastic):
Polyoxybenzylmethylenglycolanhydride, otherwise known as bakelite, and Tenite were the most prominent steering wheel cover materials before the introduction of steering wheel wraps and polyurethane.
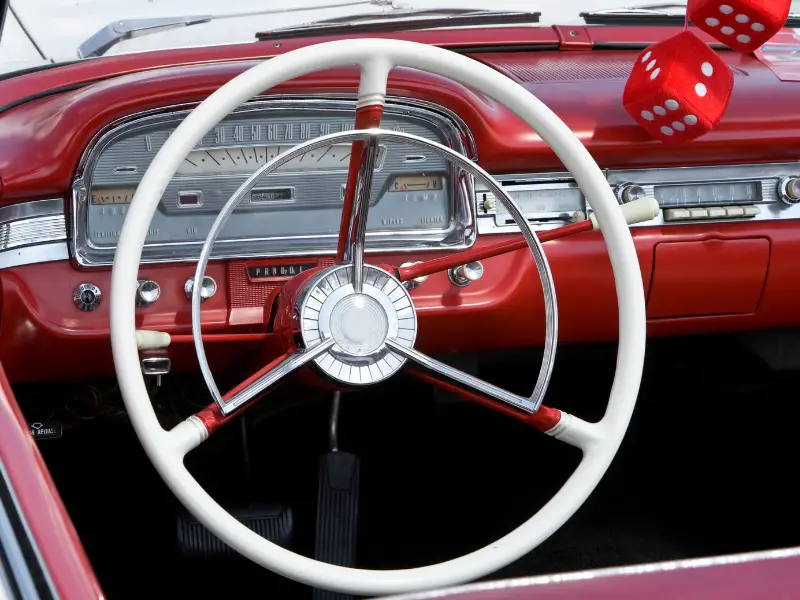
Bakelite was the first-ever plastic produced. It was invented by a Belgian chemist, Leo Baekeland. Baekeland combined the 2 synthetic materials, formaldehyde and phenol, under heat and pressure to produce the first-ever plastic, Bakelite.
Tenite steering wheels, which became a craze in the 40s, were very attractive at the time. Its smooth and glossy texture looked very aesthetically pleasing, even today. It was produced in many rich colors and textures, making the design of steering wheels very customizable. Due to this, Tenite was “thee” steering wheel material for higher-end luxury vehicles, while Bakelite was for lower-end vehicles.
Bakelite and Tenite are poor conductors as they’re resistant to heat and electricity. These properties were very important at the time because it was unsafe to use a bare metal steering wheel at the time.
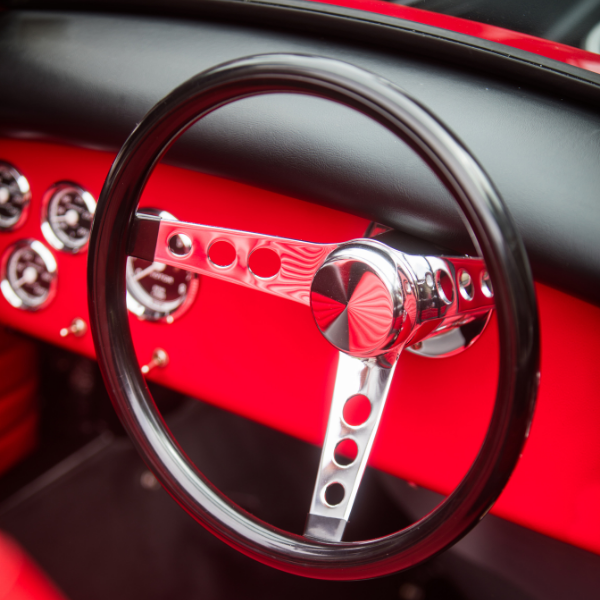
Bakelite and Tenite are very stable materials and do not react to chemicals. They are both hard, resistant to scratches and, like most other plastics, do not corrode or rust and thus are very durable materials for a steering wheel.
Today, many vehicles still use these plastics as a cover for the armature of the steering wheel, except that it is now an under-material for the leather/Suede/Alcantara-wrapped steering wheels. There are longer any vehicles that use bakelite as a steering wheel grip anymore.
Polyurethane:
Polyurethane is a very common plastic. It is an everyday part of our lives. It is the material that makes up our mattresses, dish sponges, seats, and yes, even your steering wheel!
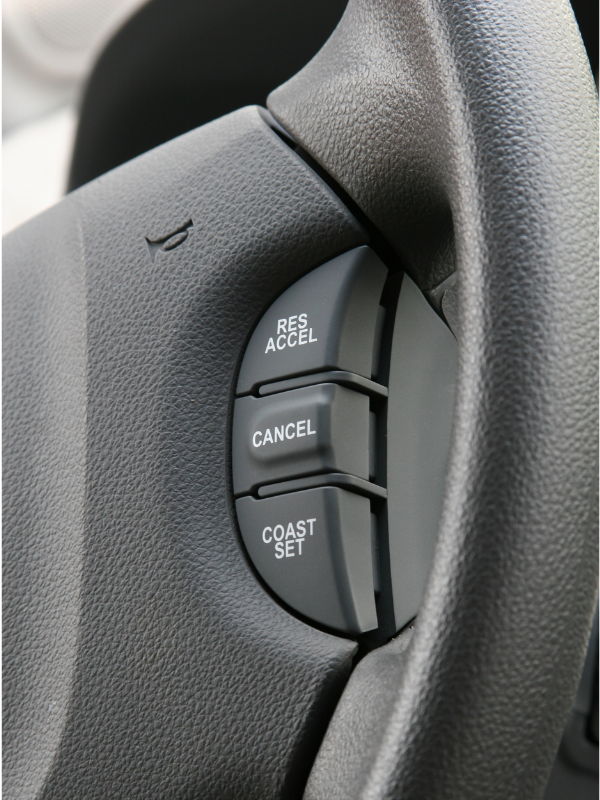
Polyurethane steering wheels became prominent in the 1980s, and onwards. As vehicles progressed to drive at higher speeds, driver safety become more of a pressing issue. Manufacturers were testing for ways to minimize injuries in the event of accidents.
Polyurethane steering wheels are dense foams, not hard like Bakelite steering wheels, so they can absorb some of the impacts in the event of an accident. This was important during a time when airbags were not a standard feature included in consumer vehicles.
While it did not look as good as Tenite steering wheels, a polyurethane steering wheel had a much better grip than hard plastic steering wheels. Polyurethane’s production process was also very efficient and cost-effective, and it became the standard steering wheel wrapping material ever since.
The polyurethane used in a steering wheel is made by mixing 2 polyurethane chemicals which then react and expand to form a dense foam. The steering wheel armature is placed in a mold cavity, and the 2 polyurethane chemicals are injected into the mould cavity. The foams react and form densely within the mold.
Polyurethane does not fare as well as the previously discussed materials when exposed to sunlight, so a protective layer of coating/painting is sprayed along the walls of the mold cavity to encase the polyurethane foam. This spray would also double as a non-adhesive so that the polyurethane foam would not stick to the cavity material.
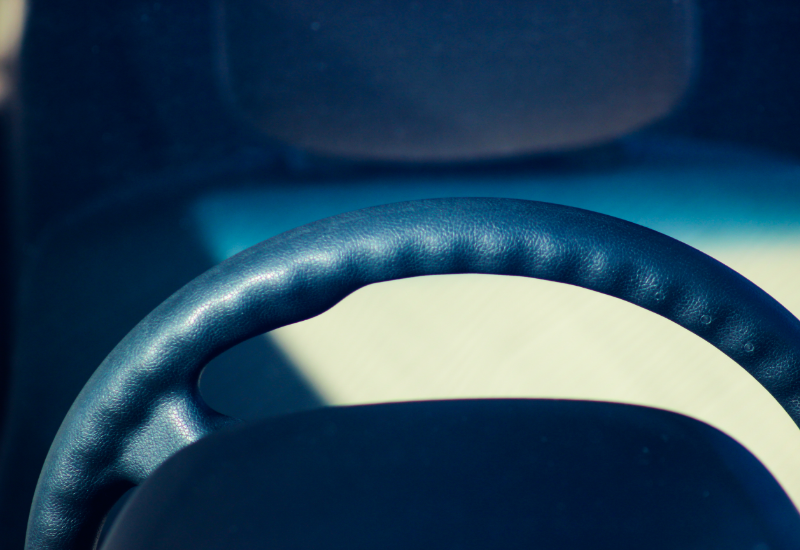
Polyurethane is still being used in many steering wheels today. However, as manufacturers continue to standardize more luxury features in their vehicles, more and more vehicles are coming with leather-wrapped steering wheels as standard, leaving polyurethane steering wheels limited to used cars, lower-end cars, and the aftermarket steering wheel industry.
Wrap Material
Leather:
While exclusive to higher-end vehicles in the past, leather steering wheels have now become the most common steering wheel material today. Many manufacturers, as a standard feature, wrap their steering wheels in leather material as consumers have more money to spend and as leather has increasingly become less expensive to produce.
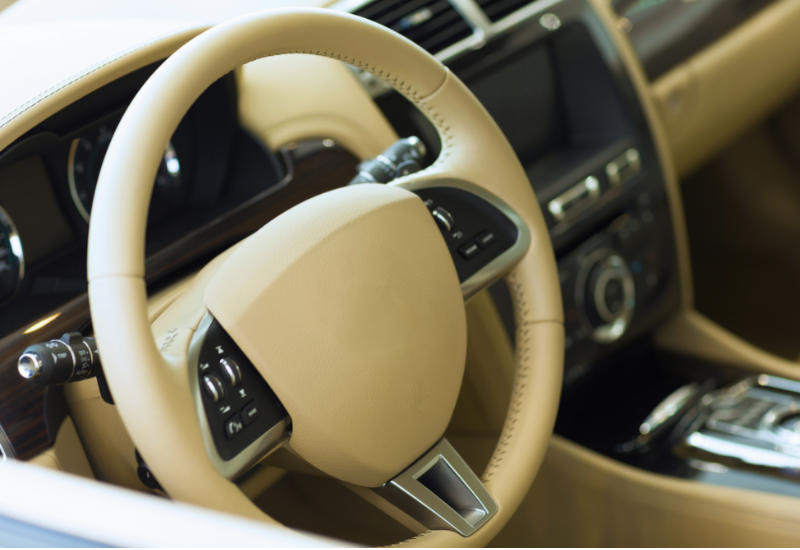
Most manufacturers spray a protective coating onto their leather steering wheels. These protective coatings greatly enhance the durability of the steering wheel, making it less susceptible to UV rays, hand oils, discoloration, and scratching. Pigmented or Teflon-coated leather is used in most leather steering wheels.
Leather steering wheels last a very long time and are very easy to maintain.
Leather is typically wrapped and stitched around a thin hard plastic, though, in some manufacturers that still produce polyurethane steering wheels in their base model vehicles, it can be wrapped around the polyurethane as an upgrade.
Suede:
Suede, also known as napped leather, is another form of leather. It’s the underside of animal skin, which has a fuzzy texture. It carries much of the same applications as leather; including steering wheel wraps. Much like leather, it is stitched around the underlying plastic which covers the steering wheel’s armature.
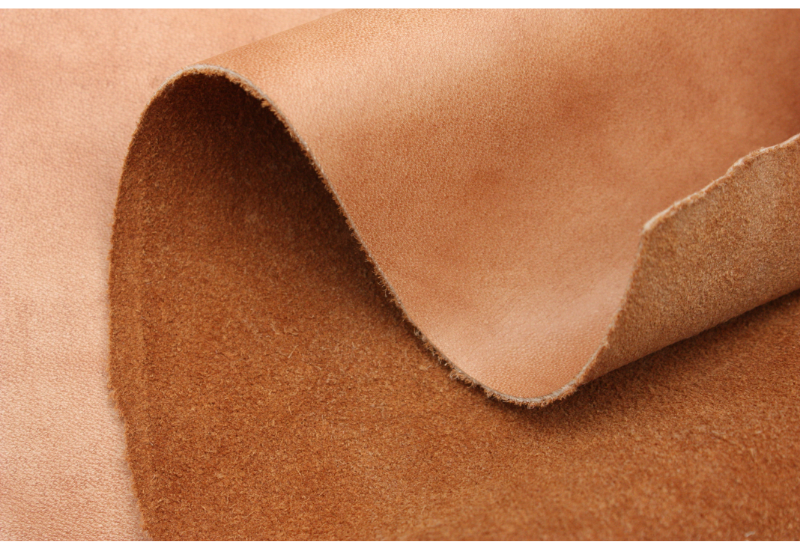
Suede is considered to be a luxury material. It is generally just as expensive to produce as leather and can be made from any of the same animal skins used to produce leather. The manufacturing process of suede can be seen here.
Suede gained popularity in automotive steering wheels because of its soft and fuzzy texture. It is most commonly seen in some higher-end vehicles and performance cars. However, the vast majority of vehicles with suede interiors are most likely made with a synthetic suede, mainly Alcantara.
Alcantara:
Alcantara is a synthetic material, made to mimic suede. It was first invented at Toray Industries in Japan, by a scientist named Miyoshi Okamoto, during the 1970s.
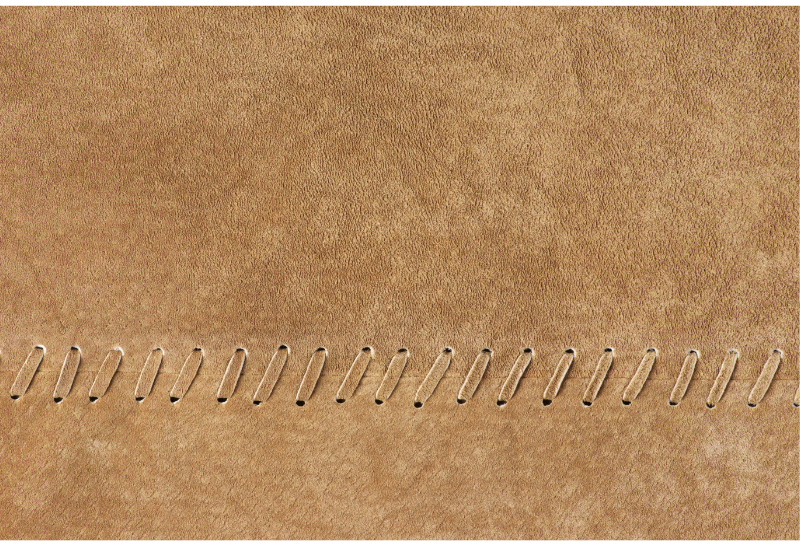
Alcantara is the most common synthetic suede material used in cars, however, some brands do use other synthetic suedes, like microsuede and Ultrasuede. Alcantara and suede share many of the same properties, although there are some key differences.
The production of Alcantara is much cheaper when compared to authentic suede, all the while being more durable and lighter. It is also eco-friendlier as it does not involve the use of animal hides. With all of these factors considered, Alcantara is used far more than suede is in the automotive industry as it offers better benefits with little drawback.
Best steering wheel material?
Today, most cars come with a wrapped steering wheel. So, from a consumer’s perspective, the best steering wheel material will typically come down to the covering material, which is the material the driver is coming into contact with, besides the buttons.
Leather steering wheels are generally more durable than Alcantara while also being far easier to clean. Alcantara, on the other hand, feels much better to the touch and provides more grip to the driver; It is for this reason that many race car drivers may choose Alcantara over leather for their steering wheels.
Leather vs. Alcantara vs. Suede steering wheels?
I’ve recently conducted an online survey, in which the respondents were mostly auto-detailers, I had polled the participants on what their preferred steering wheel cover/wrap material was.
Given the respondents were mostly auto-detailers, the difficulty of maintenance was a significant determining factor for the respondents, as they had experience with all of the materials. The results of the survey were as follows:
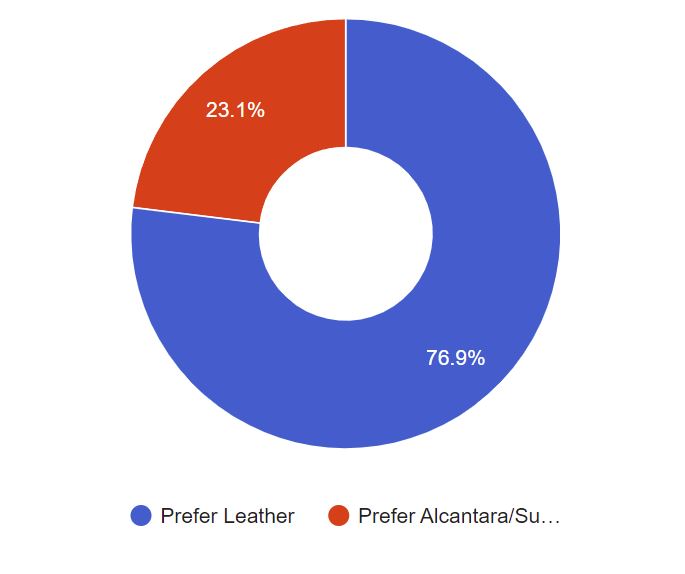
At 77%, the majority of the respondents chose a leather steering wheel while only 23% preferred Alcantara or suede.
Alcantara and suede were grouped because most can not distinguish the two. The vast majority of suede steering wheels are Alcantara, so most users would not have had experience with suede.
The main reason for this result is because leather is far easier to clean, and more durable at that. The respondents pointed out that a leather steering wheel will almost always have a protective coating on it. So, most of the time, you would just be cleaning the leather coating.
Suede, on the other hand, is not very easy to clean. The respondents stressed how careful one must be when cleaning a suede steering wheel. Alcantara is easier and more durable than Suede, but both pale in comparison to leather, in both aspects.
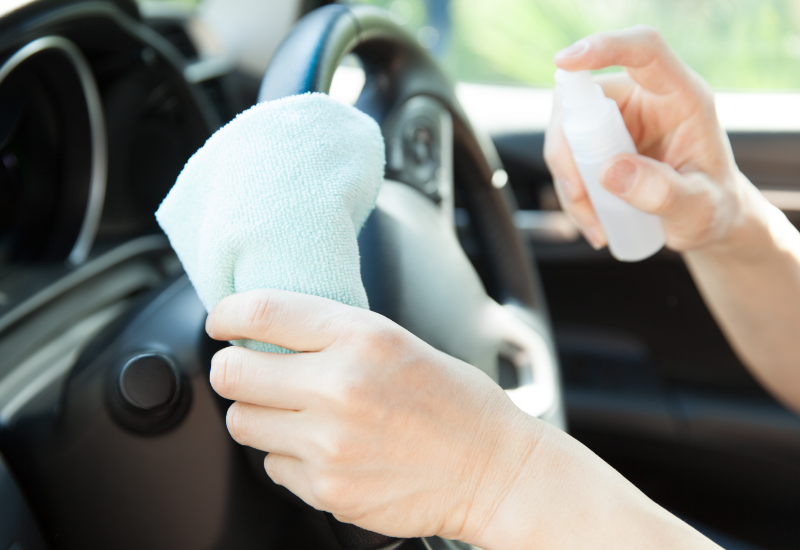
Alcantara steering wheels are lighter and much grippier than leather steering wheels. That is why the vast majority of Alcantara usage in steering wheels is limited to performance cars, where grip is very important.
Why are steering wheels designed the way they are?
The design of the steering has progressed very far and will continue to do so. Many factors go into the design of a steering wheel. Steering wheels are designed the way they are to maximize practicality and safety.
The rim-like design of a steering wheel is meant to allow the driver to rotate the wheel over many circulations without having to dislocate his/her hand in and out of the wheel. The rim also allows the driver to see the dashboard instruments.
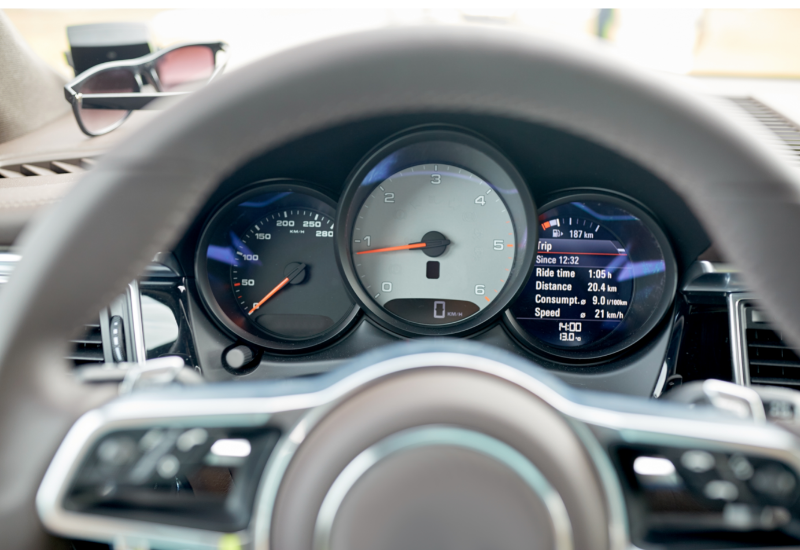
Can I change my steering wheel material?
Unless you get an aftermarket steering wheel, it is unlikely you can change the structural material in your steering wheel. Even then, if your steering wheel already has an airbag, an aftermarket steering wheel would be illegal in most developed countries.
Changing or adding a cover/wrap to a steering wheel is perfectly doable. This would involve stitching the steering wheel with either an Alcantara or leather fabric. It can be wrapped on top of a polyurethane steering wheel. If there is already a wrap, it should be removed and replaced with the new wrap.
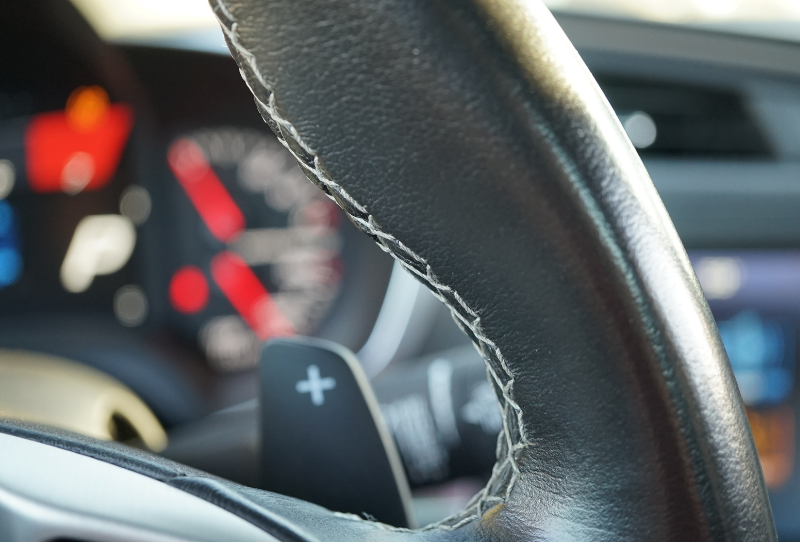
Changing your steering wheel material can be relatively inexpensive and can have a long-lasting effect. However, the process of stitching the leather or Alcantara to your steering wheel can be time-consuming.